Алюминий-магний қорытпасынан құйылатын қалыпқа арналған термиялық өңдеу процесін талқылау
Алюминий-магний қорытпасынан құйылатын қалыптардың жұмыс жағдайлары мен талаптарына сәйкес, бұл мақалада қалыптың сипаттамалары талданған. термиялық өңдеу мен жалпы процестерді егжей -тегжейлі қарастырады және термоөңдеу процесінің техникалық сипаттамаларының ақылға қонымды тұжырымы зең бетінің қаттылығын, тозуға төзімділігін, өзектің беріктігі мен қаттылығын қамтамасыз етеді және металл сұйықтығының коррозиясын болдырмайды. Пішінге жабысу қалдықтардың жылдамдығын тиімді төмендетуге және қалыптың қызмет ету мерзімін едәуір ұзартуға мүмкіндік береді.
Алюминий-магний қорытпалары тығыздығы төмен және беріктігі жоғары болғандықтан кеңінен қолданылады. Олардың ішінде алюминий-магний қорытпасын құю технологиясы озық кесу процесі ретінде жоғары өндірістік тиімділікке, шикізатты үнемдеуге, өндіріс шығындарын төмендетуге, өнімнің жақсы өнімділігіне және жоғары дәлдікке ие. Негізінен электроникада, автомобильдерде, қозғалтқыштарда, тұрмыстық техникада және басқа салаларда қолданылады, кейбір жоғары өнімді, дәлдігі жоғары, беріктігі жоғары алюминий-магний қорытпасынан жасалған өнімдер ірі ұшақтарға, кемелерге және салыстырмалы түрде басқа салаларға қолданылады. жоғары техникалық талаптар.
Алюминий-магний қорытпасынан құйылатын қалыптардың жұмыс жағдайлары мен өнімділік талаптары
Алюминий-магний қорытпасынан құюға арналған қалып-бұл құю машинасында алюминий-магний қорытпасын құю үшін қолданылатын қалыптау қалып. Алюминий қорытпасының балқу температурасы 600 ~ 750 ℃, ал магний қорытпасының балқу температурасы 600 ~ 700 ℃. Жұмыс бетінің температурасы әдетте 500 ~ 600 ℃ дейін көтерілуі мүмкін. Қуыстың, мандрельдің және саптаманың беттері температураның қатты ауытқуларына ұшырайды, ал қалыптың беті термиялық шаршау жарықтарына бейім. Сонымен қатар, алюминий-магний қорытпасы құю процесінде қалыптың бетіне оңай жабысады, бұл құю өндірісінің үздіксіз жұмысына әсер етеді. Сұйық алюминий-магний қорытпасы қалып бетіне күшті эрозиялық әсер етеді. Сондықтан, алюминий-магний қорытпасынан құйылатын қалыптарды өндіру үшін, қалып материалы жоғары температура тұрақтылығына және шамамен 600 ° C суық пен ыстыққа төзімділікке, жоғары температураға, жоғары қысымға, жоғары жылдамдыққа жақсы қарсылыққа ие болуы қажет. және сұйық алюминий-магний қорытпаларының эрозияға төзімділігі жоғары. Пішіннің беріктігі мен беріктігі, сонымен қатар қалыптың материалдық әлеуетін пайдалану және қалыптың қызмет ету мерзімін жақсарту үшін дұрыс термиялық өңдеу қажет. Қазіргі уақытта қалып өндірісінде кеңінен қолданылатын алюминий-магний қорытпасынан құйылатын шойын болатына мыналар жатады: 3Cr2W8V болат, 4Cr5MoSiV1 болат, 4Cr3Mo3SiV болат, 4Cr5MoSiV болат және 4Cr5Mo2MnSiV1 болат және 3Cr3Mo3VoXNUMXVoXNUMXV.
Алюминий-магний қорытпасынан құйылатын қалып өндірісінің технологиялық бағыты
Алюминий-магний қорытпасынан құюға арналған қалыптың өндіру процесі: бланкировка → соғу → сфероидті күйдіру → өңдеу → сөндіру, шыңдау → жөндеу, тегістеу, жылтырату → азоттау (нитокарбуризация) → құрастыру және қолдану.
Алюминий-магний қорытпасынан құйылатын қалыптың өңдеу процесін нығайту және қатайту
Алюминий-магний қорытпасынан құйылатын қалыптың қатайтатын өңдеуі болаттың құрылымын қалыптың қажетті құрылымы мен өнімділігін алу үшін өзгерту болып табылады. Термоөңдеу процесінің ерекшеліктерін анықтау үшін термиялық өңдеу форманың формасына, пішініне, өлшеміне және күрделілігіне негізделуі керек.
3.1 Алдын ала термиялық өңдеу
Қалыпты алдын ала термиялық өңдеу үш процесті қабылдай алады: үздіксіз күйдіру, изотермиялық күйдіру және сөндіру және термиялық өңдеу. Мақсаты - болаттың беріктігі мен беріктігін жақсарту үшін соңғы термиялық өңдеуге дейін біркелкі құрылымды және дисперсті карбидті алу. Үздіксіз күйдіру процесі салыстырмалы түрде қарапайым, сонымен қатар түйіршікті перлит құрылымын алуға болады. Күрделі пішіні мен жоғары талаптары бар құюға арналған қалыптар үшін изотермиялық күйдіруді гранулярлы перлит құрылымын алу үшін қолдануға болады.
3.2 Өшіру және алдын ала қыздыру
Шойын құюға арналған болат негізінен жылуөткізгіштігі нашар жоғары легирленген болат. Алдын ала қыздыру шаралары көбінесе сөндіру мен жылыту кезінде қабылданады. Алдын ала қыздыру мен температураның саны шойын болатының құрамына және қалыптың деформациясына қойылатын талаптарға байланысты. Сөндіру температурасы төмен, пішіні қарапайым және деформацияға қойылатын талаптар төмен қалыптар үшін сөндіру мен жару кезінде қыздыру кезінде алдын ала қыздыру (800 ~ 850 ℃) қажет. Жоғары температуралы сөндіру, күрделі пішіндер мен деформацияға жоғары талаптар бар қалыптар үшін қайталама алдын ала қыздыру қажет (600-650 ° C, 800-850 ° C). Мақсаты - қыздыру процесінде пайда болатын кернеуді азайту және сонымен бірге қалыптың жалпы құрылымын біркелкі ету.
3.3 Жылытуды сөндіру
Шойын құю формасының қыздыру температурасы әрбір болат маркасының сөндіру қыздыру сипаттамасына сәйкес жүзеге асырылуы мүмкін. Мысалы, 3Cr2W8V болатының сөндіру температурасы 1050 ~ 1150 ℃, ал H13 болатының сөндіру температурасы 1020 ~ 1100 ℃ құрайды. Екі болаттың сөндіру температурасын жоғарылату құйма қалыптың жоғары температуралық беріктігі мен термиялық шаршауға төзімділігін арттыруы мүмкін, бірақ бұл қалыптың деформациясын арттырады. Тұзды ванна пешінде қыздырғанда, қалып бетінде тотығу декарбуризациясын болдырмау үшін жақсы тотықсыздандыратын барий хлориді тұзды ваннасын қолдану керек, ал тотықсыздандыруды жиі жүргізу қажет. Қораптық типтегі қарсыласу пешінде қыздыру кезінде қорғаныс атмосферасын қабылдау керек; немесе қаптамадан кейін жалпы қорап түріндегі қарсыласу пешінде қыздыру. Карбидтердің толық еруін қамтамасыз ету, біркелкі аустенитті алу және жақсы жоғары температуралық өнімділікке қол жеткізу үшін, құюға арналған қалыптардың сөндіру және қыздыру уақыты тиісті түрде ұзартылуы керек. Әдетте, тұзды ванна пешіндегі қыздыру ұстау коэффициенті 0.8-1.0 мин/мм құрайды.
3.4 Суыту
Мұнайды сөндіру жылдамдығы жоғары және жақсы өнімділікке қол жеткізуге болады, бірақ деформация мен крекинг үрдісі үлкен. Әдетте маймен салқындатылған пішіндері қарапайым және деформацияға қойылатын талаптар төмен қалыптар қолданылады; пішіні күрделі және деформацияға жоғары талаптар қойылатын қалыптар үшін қалыптың деформациясы мен жарылуын болдырмау үшін иерархиялық сөндіру қолданылуы керек. Суытудың деформациясын төмендету үшін мүмкіндігінше баяу болуы керек, вакуумды төзімді пеште қыздыру мен сөндіру, газды сөндіруді қабылдауға болады. Тұзды ваннада қыздыру мен сөндіру, ал сортты сөндіру салқындаған кезде қабылдануы мүмкін. Пішін сөндірілгенде және салқындатылғанда, ол әдетте 150 ~ 200 to дейін салқындатылады, содан кейін суланғаннан кейін бірден шыңдалады. Бөлме температурасына дейін салқындатуға жол берілмейді.
3.5 Шыңдау
Құю формасының қаттылығына шыңдау арқылы қол жеткізіледі, ал қалып құю қуысының қаттылығы қалыптың ыстық және суық шаршау мерзіміне тікелей әсер етеді. Әр түрлі материалдар, әр түрлі сөндіру температурасы мен шыңдау температурасы да әр түрлі. Мысалы, 3Cr2W8V болаттан жасалған алюминий-магний қорытпасынан құйылатын қалыптың қаттылығы әдетте 42 ~ 48HRC құрайды және оның шыңдау температурасы әдетте 560 ~ 620 ℃ аралығында таңдалады, бірақ егер жоғары температуралы сөндіру қолданылса, онда температура жоғары болады. 670 ж. 1150 ° С -та сөндіруден және 650 ° С -та шыңдаудан кейінгі қаттылық 45HRC құрайды; 1050 ° C температурада сөндіруден және 650 ° C температурадан кейін қаттылық 35HRC құрайды. H13 болат алюминий-магний қорытпасынан құйылатын қалыптың қаттылығы 44 ~ 50HRC болуы қажет. H13 болатының екінші қатаю шыңы 500 ℃ шыңдау кезінде пайда болады, бірақ шыңның мөлшері сөндіру температурасына байланысты. Жылыту температурасы әдетте 560 ~ 620 is құрайды. Жылыту 2-3 рет жасалуы керек. Бірінші шыңдау температурасы төмен болуы мүмкін. Бірінші шыңдаудан кейін қаттылық мәнін өлшеңіз. Егер қаттылық талаптарына қол жеткізілсе, қаттылық төмендемеуі үшін температураны 20 ~ 30 by төмендету керек. Егер қаттылық тым жоғары болса, қаттылық талаптарына сәйкес қаттылық температурасын сәйкесінше реттеңіз. Үшінші шыңдау - қаттылықты жақсарту, шыңдау температурасы екіншісінен жоғары болуы керек
Екінші реттік температура 30 ~ 50 ℃ төмен. Шыңдау мен ұстау уақыты сөндіру кезінде пайда болатын кернеуді жоюға және көгеру сызаттарының пайда болуын төмендетуге жеткілікті болуы керек. Әрбір шыңдау үшін ұстау уақыты 2 сағ, ал үлкен қалыптарды ұстау уақыты сәйкесінше ұзартылады. Сөндіруден кейін шойын құю матрицасының жоғары жылу кернеуі мен микроқұрылым кернеуіне байланысты, штамп әдетте 150-200 ° С дейін салқындағаннан кейін бірден шыңдалады.
Алюминий-магний қорытпасынан құйылатын қалыптың бетін нығайту процесі
Сөндіру мен шыңдаудан кейін алюминий-магний қорытпасынан құйылатын қалыптың беткі қаттылығы аса жоғары емес. Қалып бетінде жоғары қаттылық пен тозуға төзімділік алу үшін, негізгі бөлігі әлі де жеткілікті беріктік пен қаттылықты сақтайды және алюминий-магний қорытпасынан құйылатын қалыптың жабыспайтын қасиеттерін жақсарту үшін, беткі азоттау немесе нитрлеу қалыпта орындауға болады. Көмірқышқылмен емдеу.
4.1 Нитридті өңдеу
Азоттау - бұл болат бетін азоттаудың термиялық өңдеу процесі, оның үстіңгі қабатындағы азот концентрациясын жоғарылату. Азоттаудың мақсаты-құйма бөлшектерінің деформациясын азайту, бетінің қаттылығын, тозуға төзімділігін, тозуға төзімділігін және алюминий-магний қорытпасынан құйылатын қалыптардың ұстауға төзімділігін жақсарту, қалыптың атмосфераға және қатты қызған буға қарсы коррозияға төзімділігін жақсарту, және жұмсартуға төзімділікті жақсартады. Шұңқыр сезімталдығы. Қатты азоттау, сұйық нитраттау және газды азоттау - азоттаудың кең тараған әдістері. Ионды азоттау, вакуумды азоттау, электролиттік азоттау және жоғары жиілікті нитрлеу сияқты жаңа технологиялар азоттау циклін едәуір қысқартады, жоғары сапалы нитраттау қабатын алады және кәсіпорындардың экономикалық тиімділігін жақсартады, сондықтан олар өндірісте кеңінен қолданылады.
4.2 Нитрокарбуризация
Нитрокарбуризация-бұл аммиак пен алкогольді сұйықтықтар (метанол, этанол) және мочевина, формил желімі және тританол желімі сияқты бірге өтетін орталар. Термиялық ыдырау реакциясы алюминий-магний қорытпаларымен құйылатын белсенді азот пен көміртегі атомдарын алу үшін белгілі бір температурада жүреді. Пішіннің беті сіңгеннен кейін, ол азот негізіндегі нитокарбурлаушы қабатты алу үшін қалыптың беткі қабатына еніп, енеді, осылайша беттің қаттылығы, шаршауға төзімділігі, тозуға төзімділігі мен коррозияға төзімділігі алынады. Нитокарбуризация әдістеріне сұйық және газ әдістері жатады, ал өндірісте қолданылатын әдістердің көпшілігі газды нитокарбуризация. H13 болаттан жасалған алюминий қорытпасынан құйылатын қалып алдын ала термиялық өңдеудің екі кезеңінде 550 ℃ × 40мин және 850 ℃ × 40мин жоғары температуралы тұзды ванна пешінде қызады, 1030 at сөндіріледі, 600 ℃ температурада шыңдалады, содан кейін әсер етеді. газды нитокөміртегілейтін термиялық өңдеуге 580 ℃. Қаттылығы 900 ГВ жоғары, матрицаның қаттылығы 46 ~ 48HRC, тозуға төзімділік, шаршауға төзімділік және қалыптың коррозияға төзімділігі едәуір жақсарды, адгезия, пиллинг, сызаттар мен коррозия жоқ, бұл оның қызмет ету мерзімін тиімді жақсартады. зең.
қорытынды
Маңызды өңдеу жабдығы ретінде алюминий-магний қорытпасынан құйылатын қалыптар өнімнің сапасы мен кәсіпорынның экономикалық пайдасына тікелей әсер етеді. Тергеу мен статистика көрсеткендей, термиялық өңдеудің дұрыс жүргізілмеуінен болатын көгеру ақауы жалпы ақаулардың шамамен 50% құрайды. Сондықтан тазартатын және қатайтатын өңдеуді және бетті нығайтатын өңдеу процестерін ақылға қонымды таңдау және термиялық өңдеу процесінің техникалық сипаттамаларын қатаң бақылау зең өнімділігі мен қызмет ету мерзімін жақсартудың маңызды әдістері болып табылады. Алюминий-магний қорытпасынан құйылатын қалыптарды өндіру кезінде қалыптың жұмыс жағдайына сәйкес ақаулардың себептерін талдау және зерттеу қажет, сонымен қатар қалыптың беткі қаттылығын, тозуға төзімділігін, өзек беріктігі мен қаттылығын қамтамасыз ету үшін металды болдырмау үшін термиялық өңдеу процестерін дұрыс құрастыру қажет. сұйық коррозия мен көгеруді жабыстырады және бас тарту жылдамдығын тиімді төмендетеді, қалыптың қызмет ету мерзімін едәуір жақсартады.
Қайта басып шығару үшін осы мақаланың көзі мен мекен-жайын сақтаңыз: Алюминий-магний қорытпасынан құйылатын қалыпқа арналған термиялық өңдеу процесін талқылау
Минге Қалып құю компаниясы Құюға арналған бөлшектерді өндіруге және сапалы және жоғары сапалы жұмыс істеуге арналған (металдан жасалған құю бөлшектерінің қатарына негізінен кіреді) Жіңішке қабырғадағы кастинг,Кастингтің ыстық камерасы,Суық палата Кастинг), Дөңгелек қызмет (Die Casting Service,Cnc өңдеу,Көгеру, Кез-келген тапсырыс бойынша алюминийден құйылатын құю, магний немесе Zamak / мырыш матрицалық құю және басқа да құю талаптары бізбен байланысуға қош келдіңіз.
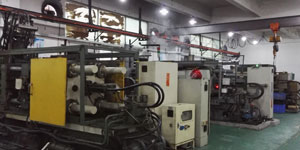
ISO9001 және TS 16949 бақылауымен барлық процестер жарылыс машиналарынан бастап Ultra Sonic кір жуғыш машиналарына дейінгі жүздеген озық құю машиналары, 5 білікті машиналар және басқа қондырғылар арқылы жүзеге асырылады. тапсырыс берушінің дизайнын жүзеге асыру үшін тәжірибелі инженерлер, операторлар мен инспекторлар тобы.
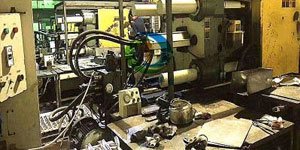
Материалдық құю өндірісінің келісімшарт өндірушісі. Мүмкіндіктерге 0.15 фунттан суық камералы алюминий матрицалық құю бөлшектері кіреді. 6 фунтқа дейін, жылдам өзгерту және өңдеу. Қосымша құнға қызметтерге жылтырату, дірілдеу, реңктерді жою, оқпен жару, бояу, қаптау, қаптау, құрастыру және құрал-саймандар жатады. 360, 380, 383 және 413 сияқты қорытпалармен жұмыс жасайтын материалдар.
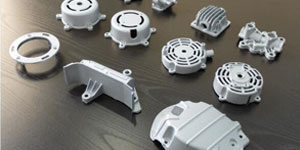
Мырыш құюды жобалауға көмек / бір уақытта инженерлік қызметтер. Дәлдікті шығаратын мырыш құю өндірісінің тапсырыс берушісі. Миниатюралық құймалар, жоғары қысымды матрицалық құймалар, көп сырғымалы қалыптар құймалары, әдеттегі қалыптарға арналған құймалар, қондырғылар мен тәуелсіз матрицалық құймалар және қуыс тығыздалған құймалар дайындалуы мүмкін. Құймаларды ұзындығы мен ені бойынша 24 дюймге дейін +/- 0.0005 дюймге дейін дайындауға болады.
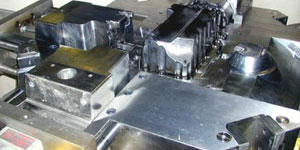
ISO 9001: 2015 сериялы магний өндірушісі сертификатталған өндіруші, Мүмкіндіктерге 200 тоннаға дейін ыстық камераға және 3000 тонна суық камераға дейін жоғары қысымды магний құймаларын құю, инструменттерді жобалау, жылтырату, қалыптау, өңдеу, ұнтақ және сұйық бояу, CMM мүмкіндіктері бар толық QA жатады. , құрастыру, орау және жеткізу.
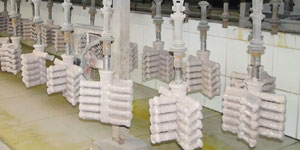
ITAF16949 сертификатталған. Қосымша кастинг қызметі қосылады инвестициялық құю,құм құю,Гравитациялық құю, Жоғалған көбік құю,Орталықтан тепкіш құю,Вакуумдық құю,Тұрақты құйма құю, .Қабілеттерге EDI, инженерлік көмек, қатты модельдеу және қайталама өңдеу жатады.
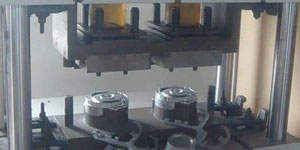
Casting Industries Бөлшектер үшін кейс-стади: Автомобильдер, велосипедтер, авиация, музыкалық аспаптар, суда жүзу құралдары, оптикалық құрылғылар, датчиктер, модельдер, электронды құрылғылар, қоршаулар, сағаттар, машиналар, қозғалтқыштар, жиһаз, зергерлік бұйымдар, әшекейлер, телеком, жарық беру, медициналық құрылғылар, фотографиялық құрылғылар, Роботтар, мүсіндер, дыбыстық жабдықтар, спорттық жабдықтар, құрал-саймандар, ойыншықтар және т.б.
Әрі қарай сізге не көмектесе аламыз?
For Басты бетке өтіңіз Құю Қытай
→Құю бөлшектері-Біз не істегенімізді біліп алыңыз.
→ туралы кеңейтілген кеңестер Құю қызметтері
By Minghe Die құю өндірушісі | Санаттар: Пайдалы мақалалар |материал Tags: Алюминий құю, Мырыш құю, Магний құю, Титан құю, Тот баспайтын болаттан құю, Жезден құю,Қола құю,Бейнені трансляциялау,Компания тарихы,Алюминийден құю Пікірлер өшірулі